The best polyurethane coatings with high applicability potential
Polyurethane liners
Research and development of new polyurethane polymers have opened the way for new production solutions.
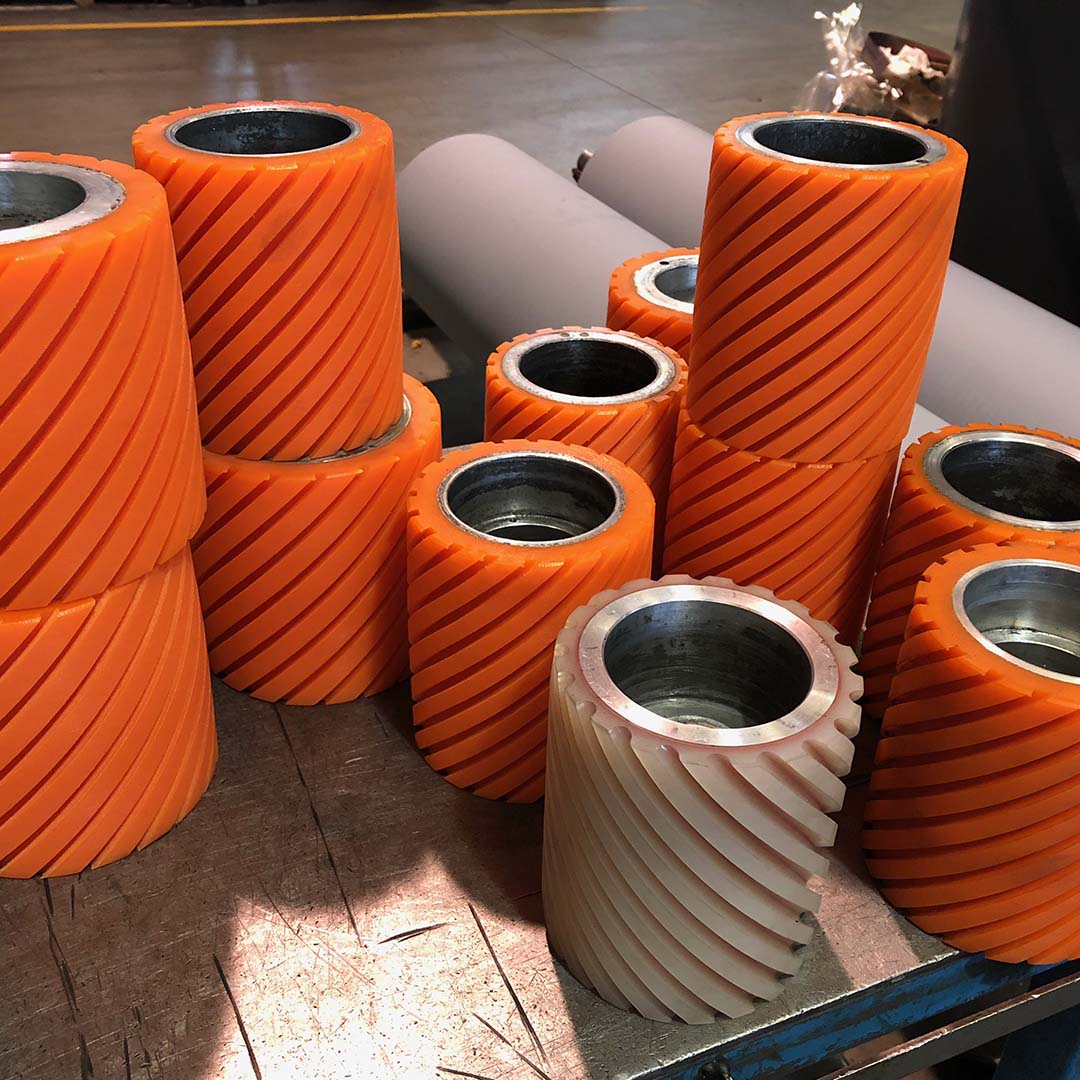
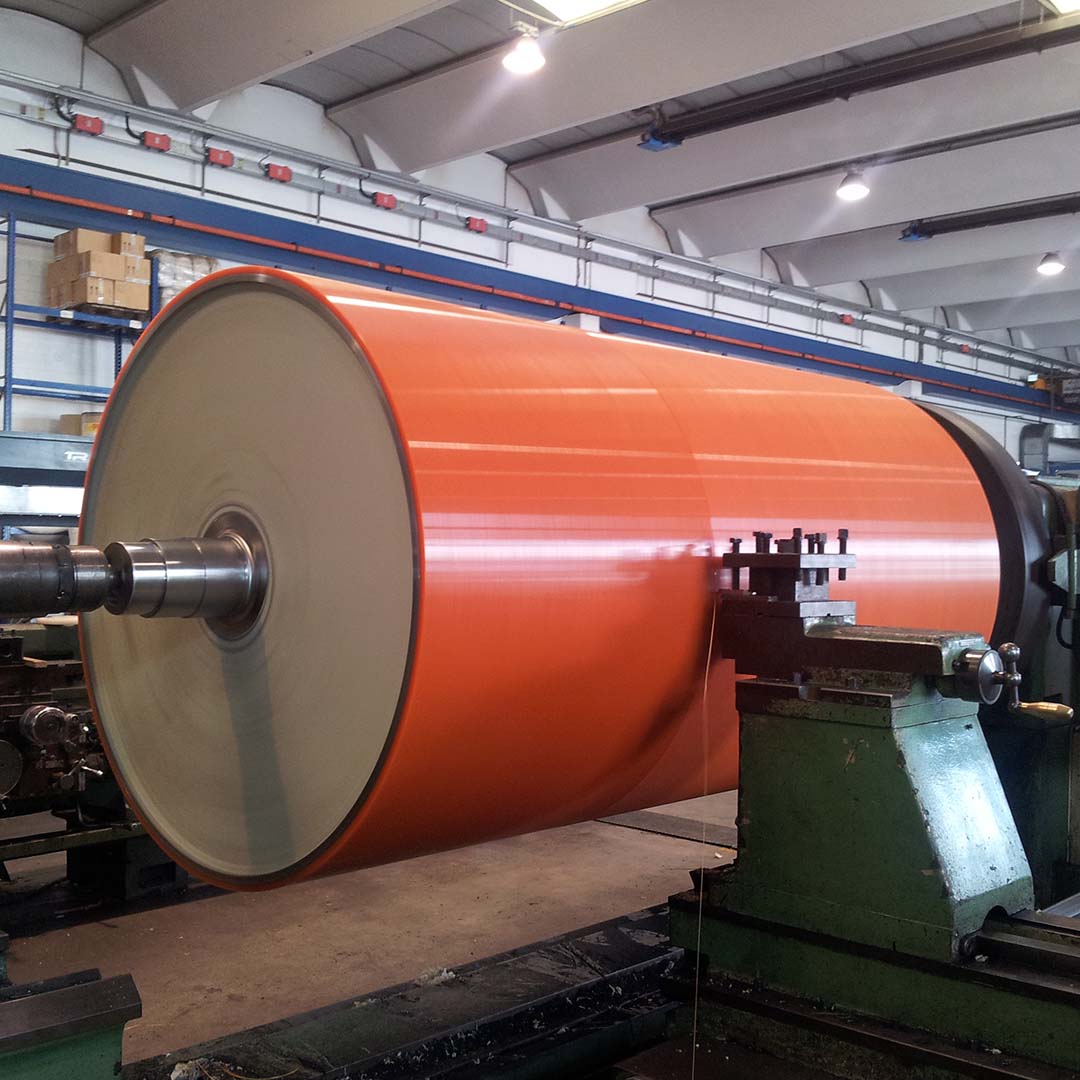
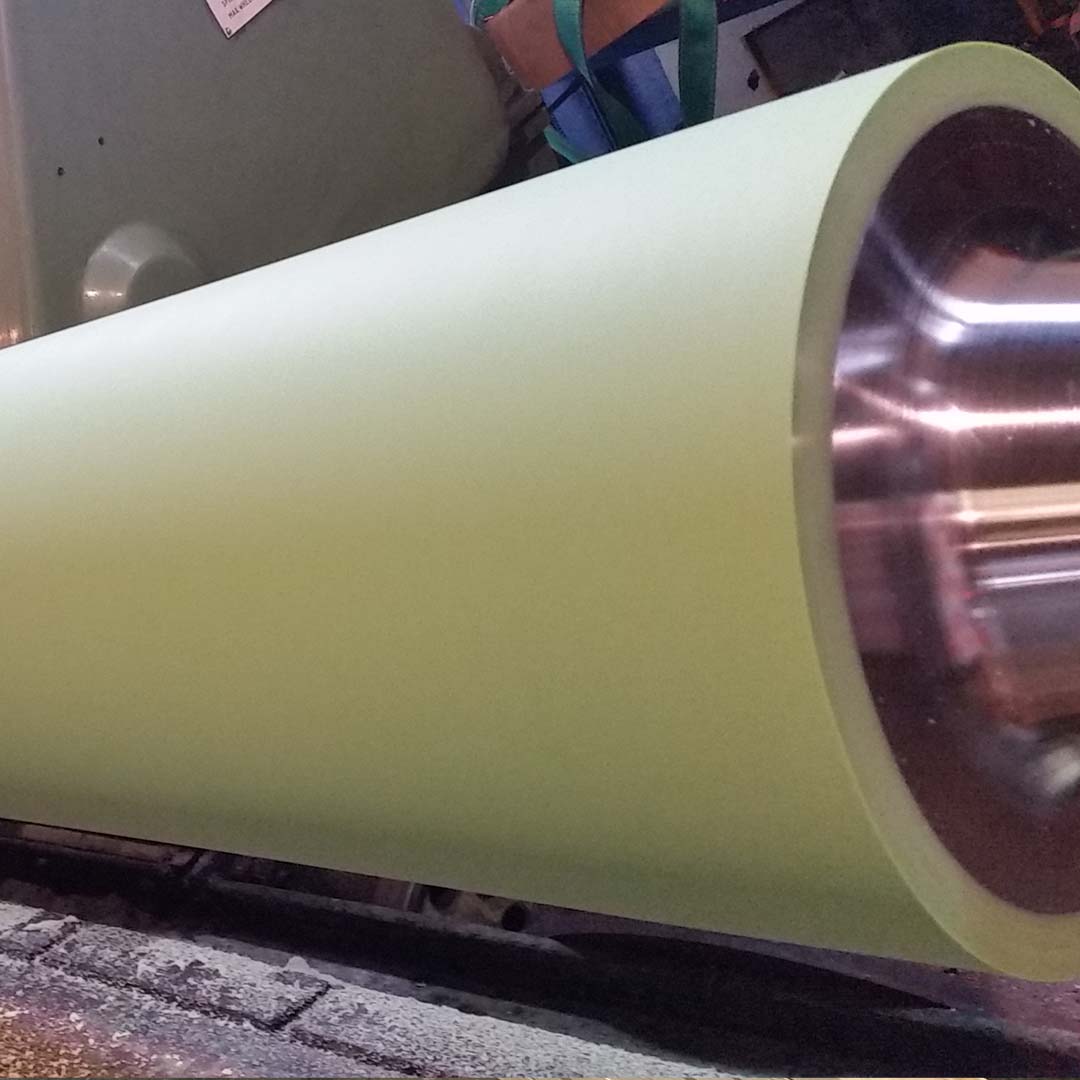
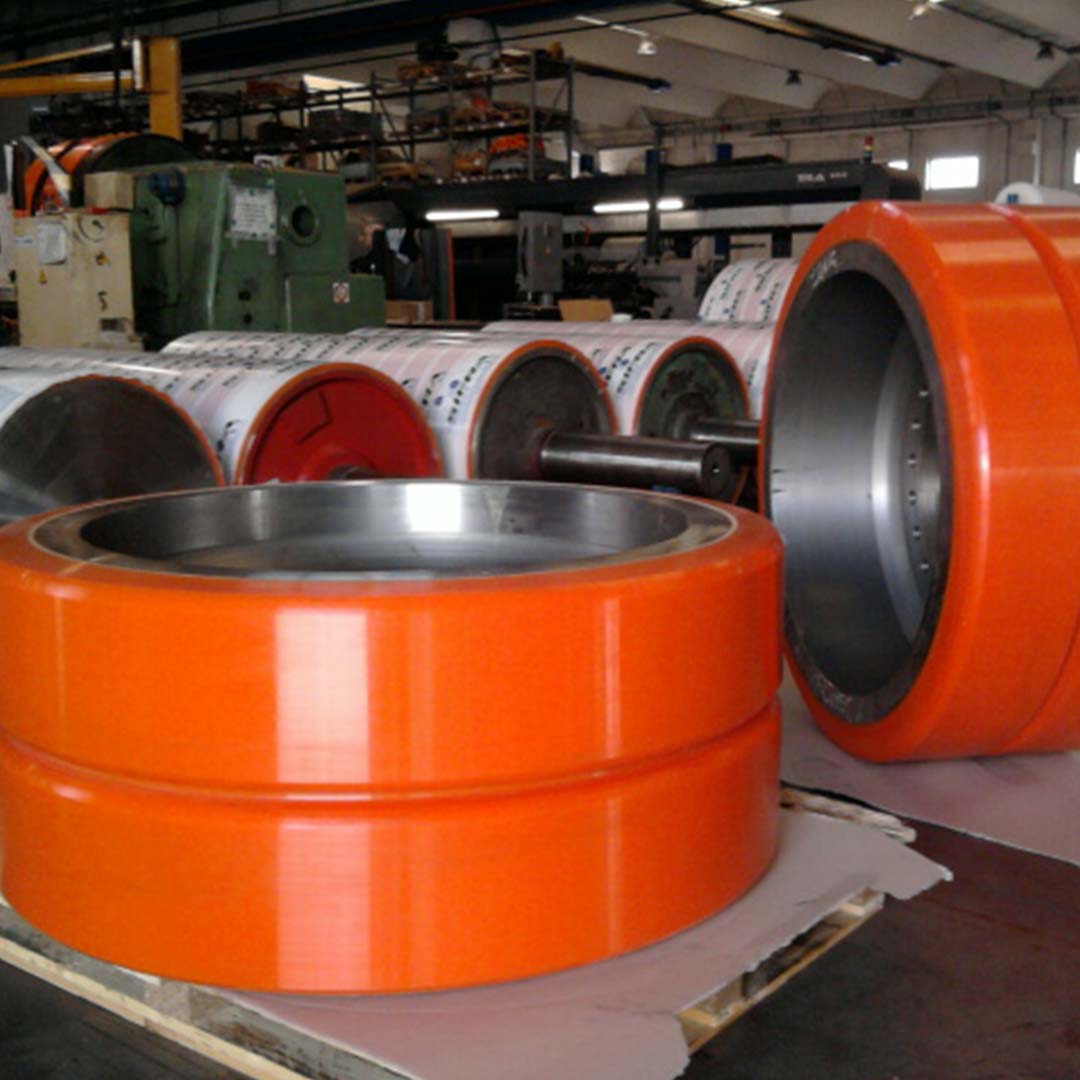
Polyurethane-coated products have a high potential for applicability and can in fact be used in the steel industry as well as in textiles, in the printing or paper industry, in the world of wood and plastics, in the oil industry up to agribusiness, and finally in packaging.
Rubber and Polyurethane: differences in performance
Compared with rubber, polyurethane products offer greater performance from a physical and mechanical standpoint: in fact, they allow a significant increase in running time and a consequent improvement in productivity.
Polyurethane is an elastomer with a high coefficient of thermal expansion: for this reason, it cannot achieve precision parameters comparable to those of metals.
The advantages of polyurethanes
Polyurethanes combine the advantages of natural and synthetic rubbers (elasticity, high elongation under load) with those of plastics (hardness, high load-bearing capacity), which is why it is exceptionally versatile, durable, flexible, adaptable and resilient.
The key peculiarity of polyurethane products is their resistance to abrasion, tearing, cutting, compression, chemicals, ozone, and finally low elastic hysteresis.
Our manufacturing process:
Sifra International follows a strict manufacturing process in polyurethane production, and all of the following steps are strictly adhered to:
- Sandblasting is the most valuable method for preparing metal surfaces and is intended to clean and roughen the area to be coated, so as to promote adhesion between adhesive and metal.
- Degreasing - this process aims to remove any traces of oil or grease from the part to be treated.
- Pickling - is a chemical dissolution operation that occurs through the use of acids or bases and has the function of surface cleaning and removing any residual dust and dirt.
- Solving - thanks to specific primers perfected by us, this process has the function of ensuring polyurethane/metal adhesion by means of a thin, homogeneous film of adhesive that is spread on the roller.
- Mold assembly - mold assembly is a process of creating one or more cavities, according to the dimensions and couplings indicated on the drawing, into which the part to be coated will be inserted.
Finally, we continue with the casting process, the polymerization, the subsequent curing of the material, turning or end grinding according to the requests of the drawing, passing then, where required, to the assembly of bearings and supports, and finally to packaging and to storage.
Cast-derived polyurethanes: superior quality
Sifra International polyurethanes are obtained by casting thus offering a superior quality in the context of ether and ester-based polymers. Sifra International is also able to offer coverings made with rotational method the technical term for the so-called “ribbon flow”.